In leathercraft, choosing the right materials and design is crucial—but equally important is knowing when and how to combine machine and hand stitching effectively. Selecting the right thread is essential to achieving both aesthetic appeal and structural integrity. This article explores how you can seamlessly blend these two stitching techniques in a single project, illustrated by a practical example: crafting a bespoke travel bag.
When creating complex products—such as luxury handbags with intricate components—using just one sewing machine type often proves inadequate. Master craftsmen frequently employ multiple sewing machine platforms to achieve optimal results: a flatbed machine for straight seams, a cylinder-bed machine for cylindrical or narrow details, and a post-bed machine for hard-to-reach, complex curves.SPOILER: Types of Sewing Machine Platforms
DETAILS: Types of Sewing Machine Platforms
Sewing machines for leatherwork are categorized based on their platform type, each designed for specific tasks:
• Flat-bed sewing machines are ideal for straight, long seams on large and flat product components.
• Cylinder-arm machines feature a narrow, horizontal cylindrical platform, convenient for round components and sewing curved seams in hard-to-reach places.
• Post-bed machines have a narrow, vertical post-shaped platform, allowing craftsmen to handle bulky components and complex curved seams with intricate geometry.
Sometimes certain elements simply cannot be machine-sewn due to equipment limitations. Components like handle attachments, intricately shaped handles, decorative features, or areas with extremely limited access require specialized equipment or an exclusively manual approach. In such cases, artisans hand-stitch not only individual elements but sometimes entire product assemblies.
Visual and Structural Differences Between Hand and Machine Stitching
Hand and machine stitching fundamentally differ in appearance and stitch formation. The shape and size of a sewing machine needle significantly influence the hole shapes in leather and, consequently, stitch appearance and direction. For example, specialty needles with various point shapes (chisel, blade, etc.) produce stitches with different angles and visual effects, achieving a machine stitch that can resemble certain hand-sewn types.
DETAILS: Needle Shapes and Stitch Appearance
Needles for machine sewing leather come with various cutting-point shapes. Needle geometry—such as wedge-shaped, diamond-shaped, and flat “blade”—determines the hole shape in the material. For instance, a “blade” needle creates flat, angled holes producing a visual effect similar to a hand-sewn “French stitch,” although stitch angle direction will differ. Thus, the choice of needle directly influences the aesthetic appearance of the stitch and the finished product.
Additionally, hand stitching requires preliminary marking and/or hole punching before sewing. Special tools such as stitch markers and stitching hole punches (diamond irons, pricking irons in French and round dent styles) are used for this purpose. Similar to machine needles, these tools vary in shape and spacing between holes. Depending on the tool’s geometry, holes may be round or angled (flat and inclined), directly affecting the look of the hand stitch. Consequently, the saddle stitch may not always have a pronounced stitch angle—its appearance depends significantly on the chosen punching tool and stitching technique.
It’s also important to note that machine sewing involves minimal mechanical stress on the thread, which immediately forms the stitch. By contrast, saddle stitching involves repeated passing of the thread through material, subjecting it to considerable tension and friction.
DETAILS: Stitch Formation Principles
• Machine stitching utilizes a two-thread lockstitch method, interlocking the top and bottom threads within the material. One thread enters from above, the other from below, forming a loop that secures the stitch.
• Hand stitching, typically saddle stitching, employs a single thread passed through each hole sequentially using two needles, independently securing each stitch, thus enhancing seam strength and durability.
DETAILS: Thread Behavior by Technique
With machine stitching, thread experiences minimal abrasion, maintaining its original properties and appearance, as it moves directly from spool to stitch with only slight friction during passage through the machine’s adjustment nodes and needle eye.
In hand saddle stitching, thread repeatedly passes through material, enduring significant stress, friction, and gradual degradation of properties and appearance.
Thus, threads for hand and machine sewing differ fundamentally in their characteristics and aren’t always interchangeable. Machine threads typically have moderate twist density, elasticity, and smooth texture. When used for hand stitching, these threads frequently unravel, tangle, or loop, losing aesthetic value and complicating the craftsman’s task. Threads specifically for hand saddle stitching, such as waxed linen, have high twist density, minimal elasticity, stiffness, and natural irregularities, making them unsuitable for machines.
To illustrate how theory translates to practice, let’s examine a specific project—the creation of a travel bag—highlighting how Xiange Twist thread allowed seamless integration of machine and hand sewing techniques.
Practical Case: Creating a Travel Bag
Disclaimer. If you’ve been following my work, you know I traditionally rely almost exclusively on hand-stitching, using MeiSi Super Fine waxed linen thread. This aligns with my detailed, deliberate craftsmanship. Seeing me use a sewing machine might come as a surprise—but it’s not a departure from principles. Rather, it’s a strategic choice driven by practicality: when certain elements simply can’t be sewn by hand, I pick the best possible tools to achieve the required quality without sacrificing aesthetics.
One Thread for Two Approaches
I rely on threads from Shenzhen Minglang Textile Technology Co., Ltd., specifically Xiange Twist and MeiSi Super Fine—two threads well-suited to both machine and hand stitching tasks.
Balance is Key
I’ve developed a simple rule: If an item can be sewn entirely or nearly entirely by hand, I choose MeiSi Super Fine—natural linen thread suitable for both manual and machine stitching. However, when forced to rely heavily on machine stitching—particularly with fabrics and large details—I opt for thread providing flexibility without needing to change material mid-project. Xiange Twist uniquely meets this need without compromise.
DETAILS: Two Threads—Xiange Twist & MeiSi Super Fine
• Xiange Twist is waxed thread composed of three twisted polyester fibers. Visually resembling linen, it provides synthetic material advantages: fade resistance (due to high-temperature dyeing), excellent tensile and abrasion strength, and suitability for melt-finished stitches. It works equally well for manual and machine stitching, available in five thicknesses and 84 colors, ideal for leather goods, sports equipment, upholstery, denim, and other demanding applications.
• MeiSi Super Fine is a natural linen thread designed specifically for machine stitching but equally excellent for handwork. Thinner and smoother than traditional linen threads, lightly waxed to reduce friction while retaining structure for saddle stitching. Ecologically dyed, UV-resistant, and water-stable. Available in four thicknesses and 98 colors—ideal for those seeking natural thread with versatile capabilities.
In this project—a travel bag—I used Xiange Twist primarily because the majority of the construction required machine stitching, particularly with the lining fabric, decisively influencing thread choice.
Materials: Exterior and Interior
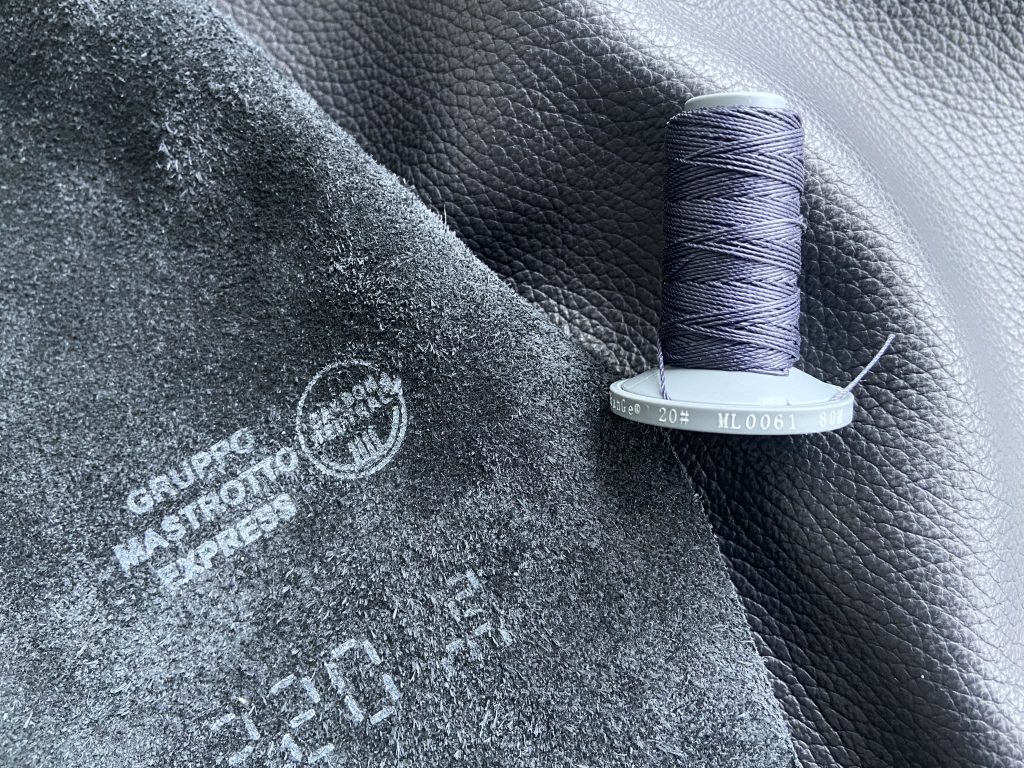
For the exterior, I selected premium Adria calf leather from Gruppo Mastrotto, Italy. Known for its robust “Dollar” grain, this leather combines elegance, flexibility, and strength, easily molded into sophisticated forms. Its deep matte navy hue emphasizes the leather’s natural texture and the bag’s sleek silhouette.
The interior is crafted from durable, heavy-duty “Oscar” fabric in a soft, natural melange tone. Produced in Spain, this blend of cotton, polyester, and linen features high abrasion resistance (35,000 Martindale cycles), and water-repellent properties. Beyond mere lining, it serves as structural support, complete with pockets, leather-trimmed zippers, and finished edges, providing both aesthetic and functional excellence.
A Project Where Every Detail Counts
This bag is quite large: approximately 55 cm long, 30 cm high, and just over 20 cm wide. Its main panel, before assembly, measured roughly 100×55 cm. Attached to it were long handle supports—nearly a meter in length—which resemble belt-like strips encircling the bag’s body.
Dimensions like these present not only design challenges but purely technical ones as well. Hand stitching requires simultaneous access to both the front and back sides, complete visual control, and the ability to manipulate the workpiece from either side. At this scale, that’s physically quite uncomfortable—after all, none of us have meter-long arms. Although I’ve previously assembled similar bags entirely by hand, for this particular project, I opted to machine-sew the handle supports. It was precisely Xiange Twist thread that allowed me to retain the aesthetics of a handcrafted stitch while benefiting from machine precision.
Despite the availability of various handle-making alternatives, I intentionally chose a manual approach for this project. Even though handles could have been machine-sewn, considering certain nuances, I consciously decided on hand stitching. This wasn’t an exception but a deliberate choice: in elements where strength, symmetry, and meticulous attention to every detail matter most, I feel more connected and precise when working by hand.
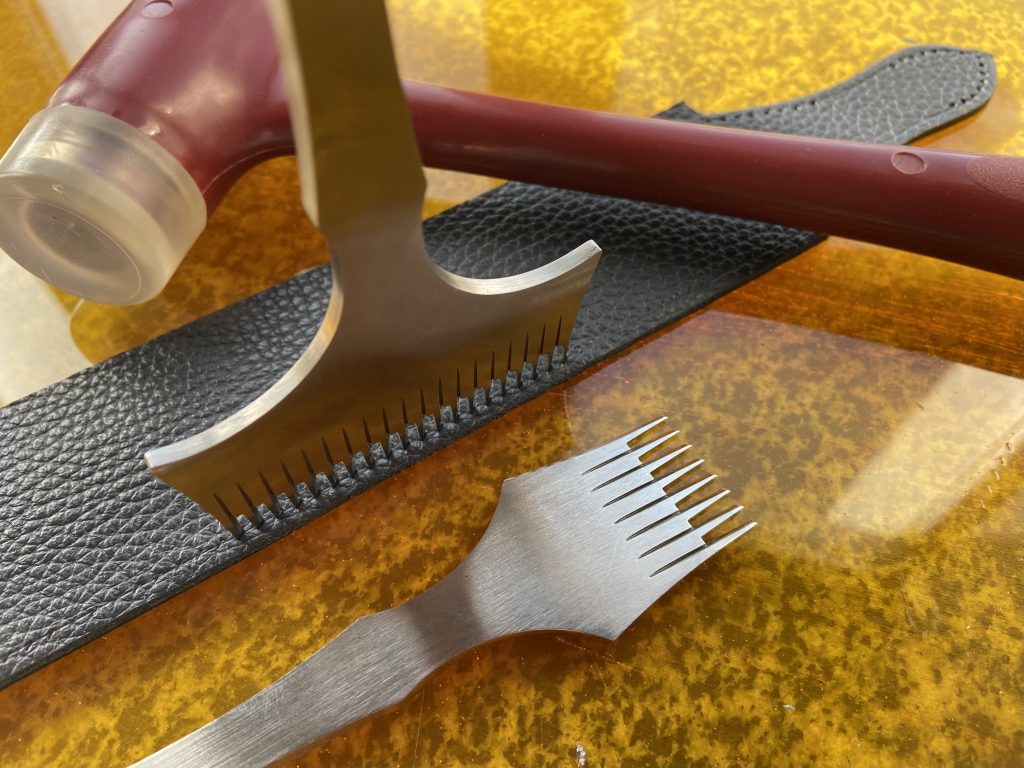
For punching stitch holes, I used a 20/8/2-tooth French-style pricking iron from Kevin Lee, with a spacing of 3,38 mm—closely matching the machine stitches used elsewhere in the bag. This tool helps maintain visual harmony even when combining techniques. The handle was sewn and attached to the bag using the traditional saddle-stitch method. This is precisely the stage where your hands need to sense and control every detail: thread tension, material alignment, and symmetry of each puncture. This step restores the rhythm of handcrafted work—its fluidity, precision, and silence. I recorded a short video to convey the feeling and demonstrate how hands effortlessly join what machines are still learning to master.
Conclusion
Combining hand and machine stitching isn’t a compromise but rather an opportunity to leverage the strengths of both techniques. Carefully chosen thread, such as Xiange Twist, serves as a connecting element that ensures not only visual cohesion but also functionality, reliability, and comfort throughout the process. This integrated approach opens up new possibilities for artisans to execute complex projects without sacrificing quality or aesthetics.
Kondratenko, V. (2025e, March 29). One thread, two techniques: combining hand and machine stitching for leather goods. V.Kondratenko. https://kondratenko.studio/blog/hand-and-machine-stitching/